ChemGrout manufactures standard and custom-built grouting equipment for various materials and capacities, specially designed to be user- friendly and trouble-free. Among them is the ChemGrout CG-680 high-pressure (HP) series, which is suitable for tunnelling, dam foundations, soil compaction and encasements, among others.
The CG-680 HP series is a high-pressure, high-capacity, skid-mounted colloidal grout machine for mixing and pumping slurries of cement, fly ash, bentonite and lime flour. It is designed to provide a continuous mixing and pumping operation, with a 0.5 cu m homogenising colloidal mixer, 0.5 cu m agitated storage tank and 120 l/min grout pump.
The high-capacity, double-acting plunger grout pump is connected directly to the agitated storage tank to provide a continuous pumping operation. The colloidal mixer is equipped with a 2X3X12 high-shear centrifugal diffuser-type pump that disperses the cementitous material down to its finest particle size to achieve complete particle wetness.
The mixing tank is also equipped with a bridge breaker to break apart the material before entering the colloidal mixer. The agitated storage tank has a variable-speed, high-efficiency paddle mixer that maintains a thoroughly mixed grout while waiting to be pumped.
Another highlight is the ChemGrout CG-550/030 Rugged HP series, which is capable of handling materials ranging from fluid slurries to heavily sanded grouts. The machine can be skid-mounted or trailer-mounted, featuring a 170-l mixing tank, 57-l or 113-l holding hopper and single-acting 3-in piston grout pump.
Each mixing tank is equipped with baffles, bag breakers, and a variable-speed, high-efficiency paddle mixer that provides rapid grout mixing. The tank outlet is a large slidegate that allows viscous grouting materials to flow quickly into the removable holding hopper.
A complete grouting system combines the CG-030 piston pump with the high-efficiency paddle mixer to provide a continuous output of material. Both mixer and pump are equipped with their own variable speed control.
Materials commonly used with the CG-030 include cement slurries, sanded cement mixes, bentonite mixes (with or without sand), most repair mortars, high-strength non-shrink grouts and self-levelling products.
The large capacity hopper is mounted above the suction housing, enabling a new batch to be mixed while the first is being pumped. This helps to provide a consistent ‘non-stop’ discharge of material, virtually eliminating the clogging of tremmie lines.
The skid-mounted model is offered in a variety of power options, and is also available in a gas/hydraulic or diesel/hydraulic trailer version. The trailer-mounted model is a fully integrated system combining mixer, pump and power system. It is road and jobsite ready equipped with leaf springs, lights and a working platform.
Asia Pacific presence
Based in Illinois, USA, ChemGrout was established in 1963 as a grouting contractor providing cement and chemical grouting field services. The company also manufactured grouting equipment for its own use. In 1969, the company began selling and renting its equipment to other contractors while maintaining its field grouting work.
ChemGrout had been involved in more than 350 projects, both large and small, before it stopped carrying out on-site work in 1978 to focus entirely on the design and manufacture of grouting equipment. The concepts of mixer-pump balance, user-friendly operation and ease of maintenance are emphasised in the design of its grouting systems, said ChemGrout. Enough technology is incorporated to maximise efficiency, yet not so much as to compromise ease of operation or maintenance.
Today, the company manufactures a variety of standard and custom-built grouting equipment to handle a diverse range of materials and capacities (from 3.8 to 284 l/min), with pressures from 3.4 to 138 bar. High-pressure pumps can manage pressures up to 138 bar and flows up to 189 l/min. The machines can be skid- or trailer-mounted with power options that include air, gasoline, diesel, electric and hydraulic.
ChemGrout has also expanded its presence globally, including in Asia Pacific. The company has established a dealer network across Southeast Asia, Australia and New Zealand, as well as Taiwan and Hong Kong.
Speaking to Southeast Asia Construction earlier this year, Joe Schatz, general manager of ChemGrout, said that he is optimistic about the future of the company in Asia Pacific. “We see widespread acceptance of our equipment throughout the region, and we continue to see infrastructure spending driving growth.”
Note: The longer version of this story has been published in the Jul/Aug 2018 issue of Southeast Asia Construction. Click here to read more.
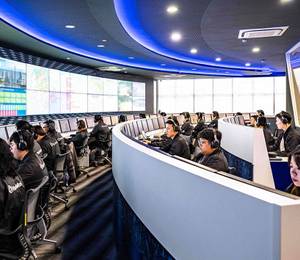
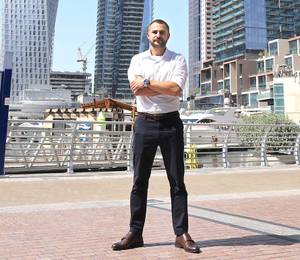
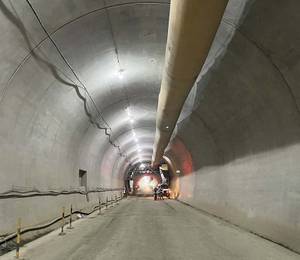
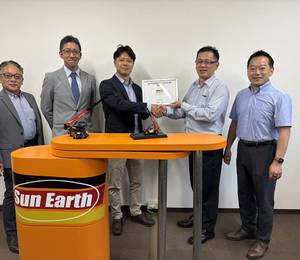

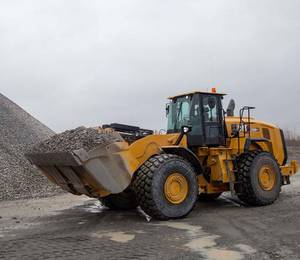

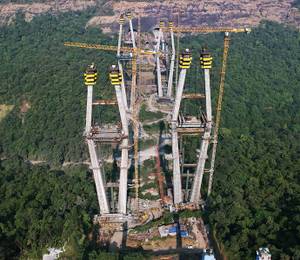
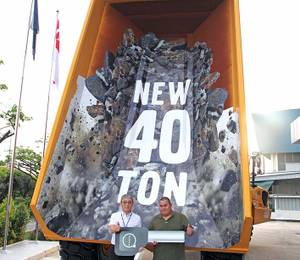
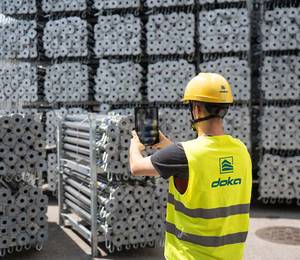