The second phase of Global Switch data centre project in Tseung Kwan O, Hong Kong - being built by Gammon Construction - requires the design and installation of a chilled-water thermal-energy storage system using a Design for Manufacturing and Assembly (DfMA) approach.
The chilled-water thermal-energy storage system provides resilience to ensure the chilled water remains available at all times, whether due to internal equipment or an external power failure. Gammon said the DfMA with full off-site fabrication could factor in the consideration of site safety, quality and duration of the construction for this vital equipment.
The final design consisted of four 175-cu-m thermal tanks, each weighing 50 t and measuring 7 m in diameter and 9 m high. Every element of the tanks – including all steel works, fencing, cat ladders, baffles, coating, thermal insulation and external cladding, and even maintenance provisions – was manufactured, preassembled and tested off-site in a DfMA factory. By doing so, Gammon eliminated the need for extensive scaffolding associated with high-level works, as well as the tremendous amount of on-site welding and painting activities, heavy lifting with complicated vertical operations, and confined space work inside the tanks.
Before work began, Gammon adopted the building information modelling (BIM) to streamline and verify the design. The BIM method was applied to structural analysis to ensure integrity and use of correct steel members, while computational fluid dynamics made certain that the components inside the tank were appropriate for effective thermal transfer of temperature profiles.
Once completed in the factory, the tanks were shipped by barge, hoisted to the roof and slid into their final positions in one action – no hot works and no high-level assembly were required, according to Gammon. Installation of the four tanks took four days, and they are also believed to be the heaviest DfMA thermal tanks installed in Hong Kong.
All images: Gammon Construction
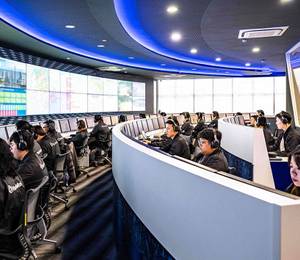
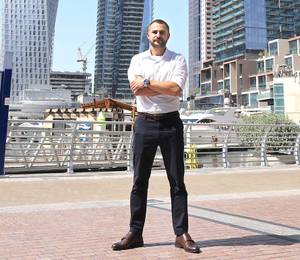
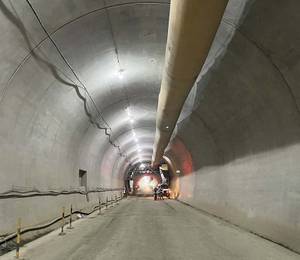
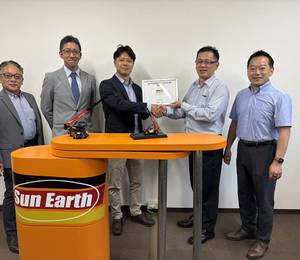

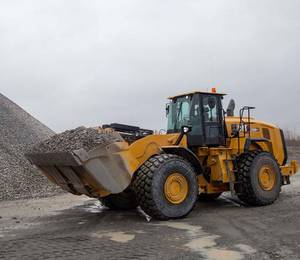

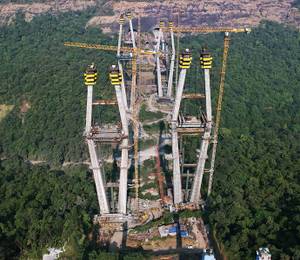
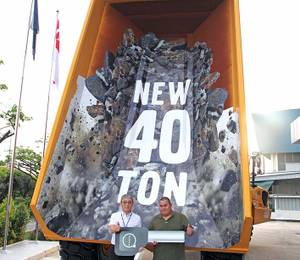
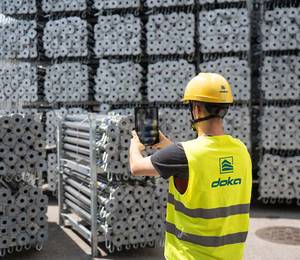