Antar Cranes Services Ptd Ltd offers a safe, productive solution for contractors who need to carry out glazing work, by using a combination of an Oktopus vacuum lifting device and a Maeda mini crawler crane (spider crane).
The Oktopus Glass-Jack GL-CC 600 DES vacuum lifting device is able to handle up to 600 kg glass elements. Manufactured by German company Wirth Gmbh, the device can lift both flat and curved glass panels as well as window components.
The suction frame of the Oktopus lifting device can be tilted hydraulically by 120°, rotated 360° and swivelled by ± 35°. All functions are operated with the help of a radio remote control. A 24-V DC operated vacuum pump generates the necessary negative pressure in the suction pads.
The Oktopus lifting device has an optical and acoustical warning equipment to indicate its deviations from the nominal condition. Even in case of complete failure of energy supply, the vacuum remains for at least five minutes in each suction pad, so that the load can be lowered safely.
The MC285CWM-3 mini crawler crane from Japanese manufacturer Maeda features a compact design, with only 750 mm in width. It provides a lifting capacity of 2.82 t x 1.4 m, maximum working radius of 8.205 m x 0.15 t, and maximum lifting height of 8.7 m (on the ground). The crane’s travel speed is 0-2.2 km/h, with a 20 degree gradeability.
The MC285CWM-3 is a new model equipped with various functions, including a programmable moment limiter, crane/outrigger interlock system, digital feedback remote control (wireless), four-fall/two-fall hook block, voice warning system and data logger.
Andrew Tan, general manager of Antar Cranes further highlighted the importance of both units as a combined solution. “Using the Maeda spider crane together with the Oktopus lifting device results in manpower savings, as users can minimise the number of workers on site. At the same time, it increases safety when handling large and heavy glass panels at height. Imagine the number of manpower needed to handle a 600 kg glass panel. Ultimately, it would make the entire project safer. Compared with the traditional method, this solution can achieve a higher productivity improvement and also more time- and cost-effective.”
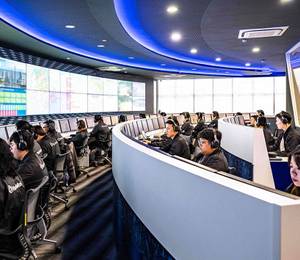
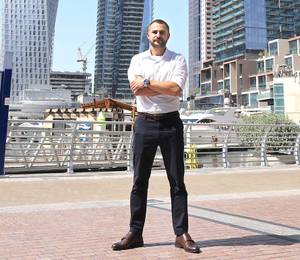
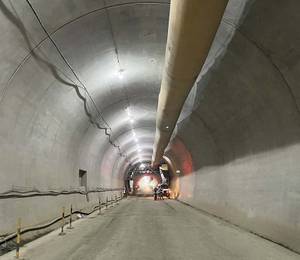
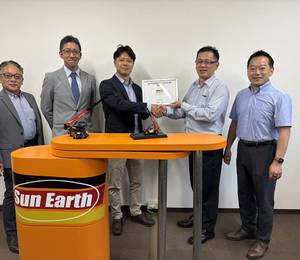

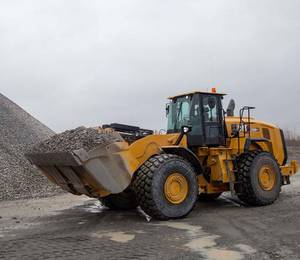

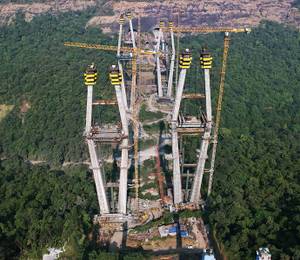
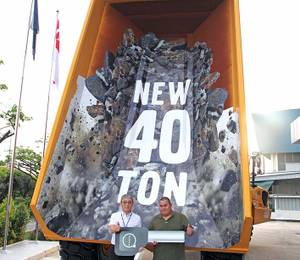
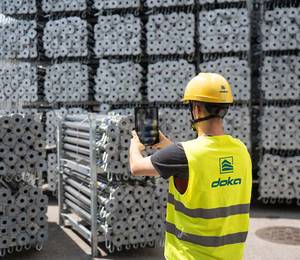