Textile was one of the major industries in Hong Kong between the 1950s and 1980s, comprising spinning, weaving, dyeing and garment manufacturing. At its peak, the industry reportedly employed more than half of Hong Kong’s total workforce, and contributed as much as 30% of the region’s GDP.
Established as a small factory in Tsuen Wan in 1954, Nan Fung Textiles factory expanded its operations rapidly. A series of cotton mills (No. 1 to 6) were built in the 1960s and early 1970s, when the textile industry reached its peak. Since 1980s, however, the industry started to decline and Nan Fung moved into property development, investment services and social initiatives. Then the mills ceased operations - Mills 1, 2 and 3 were knocked down in the 1980s, while Mills 4, 5 and 6 were turned into warehouses in 2008.
In 2014, Nan Fung celebrated its 60th anniversary and launched The Mills revitalisation project. This was inspired by the desire to preserve its roots in Tsuen Wan while giving new life to Mills 4, 5 and 6. The ultimate goal of the project was to transform and revitalise the mills into a destination for innovation, culture and learning.
Revitalisation project
Global design, engineering, and advisory company Aurecon was commissioned to support this landmark revitalisation project and was responsible for detailed design and construction administration of the mechanical, electrical and plumbing (MEP) services. Key tasks included the design and construction of new main MEP plant room while taking consideration of the existing structural elements.
All MEP plants were upgraded to meet the latest standards including transformer rooms, central chiller plant, fire protection pump room, lift, escalator, plumbing and drainage. The design of new MEP system took into consideration energy efficiency, flexibility and ease of maintenance.
Energy efficiency features including LED lighting fixtures, automatic lighting control system and free cooling were also introduced in the building. To provide flexibility to retail floors, mechanical ventilation, water supply, plumbing and drainage are designed to enable successful license application for restaurants and cafés. Web-based Building Management System (BMS) and BMS apps were developed.
The BMS app allows building management officers to monitor systems performance and change settings by using their mobile devices. When an incident occurs, officers will receive alarms, prompting response and action. In addition, energy meters were installed to monitor and record energy consumption in the public and tenant space. The data is used in energy management of the building.
Aurecon also provided building information modelling (BIM) services to facilitate the work. BIM models were used for clash detection, cost estimation and space management; thus facilitating the description and coordination between the different design consultants. This allows the architects to review the model before the start of construction, thereby reducing abortive work.
Challenges and solutions
One of the challenges was limited headroom of the building because the existing structure had to be retained. The additional steel beam used in structural strengthening work had further reduced the headroom and made design more complicated. With the help of BIM, Aurecon’s MEP designs integrated with the existing structural elements successfully, thus achieving the required headroom optimisation. In addition, the steel beam was seamlessly blended into the industrial-styled interior design.
The Gallery is one of the important areas in the building. Humidity and lighting controls were the key considerations in the design to prevent ageing of the exhibits displayed in the Gallery. Pre-action sprinkler system is also provided to prevent water damage to the valuable exhibits from water leakage. The design of the gallery’s store room was fitted with a gas flooding system and humidity control to protect the valuable exhibits that were kept in the room.
A Tenant app was developed and integrated with the BMS to provide a convenient way for tenants to apply for extension of air conditioning services. The central chiller plant operation schedule is automatically updated in the BMS once the building management office has approved the applications in the system. Technical staff are no longer required to adjust the schedule manually. The app also records the additional air conditioning service hours for billings. In this way, the building management office can easily manage the air conditioning schedule and invoicing with minimal manpower and error.
New heritage destination
With successful completion of the project in 2018, The Mills is now a destination consisting of a business incubator, experiential retail, food & beverage, design studios with training facilities, art gallery, textile industry museum, multi-purpose spaces, and a non-profit cultural institution. It is also an arts and cultural complex, a haven for innovative and start-up enterprises, and a retail space.
Regular guided tours in The Mills allow visitors to learn about the reinvention and transformation of the factory. Visitors can discover a number of visual throwbacks that have been retained, including the old bulky and rounded concrete stair banisters, sprayed-on ‘no smoking’ signs, abandoned door leaves, old scratched fire buckets, unused fabric being left on the floor, noticeable red Chinese characters of Nan Fung Mills on the outside of the buildings. All these historical elements form part of the building’s history and story.
The Mills was awarded ‘New Design in Heritage Contexts’ by UNESCO Asia-Pacific Awards for Cultural Heritage Conservation in 2019.
All images: Nan Fung Textiles Second Mill Ltd
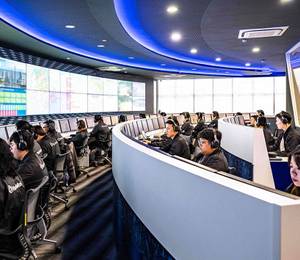
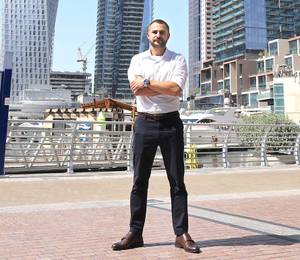
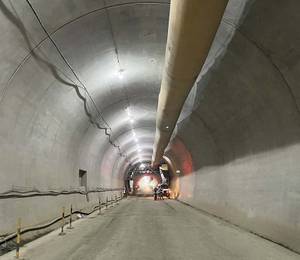
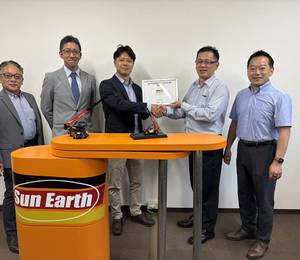

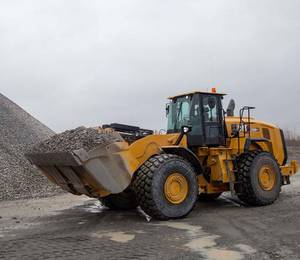

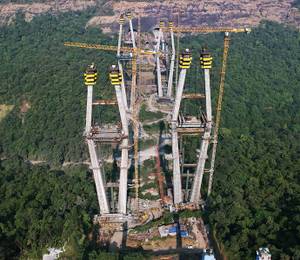
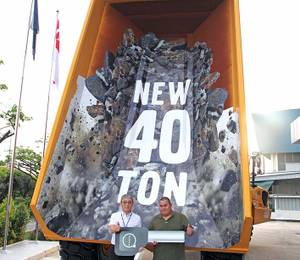
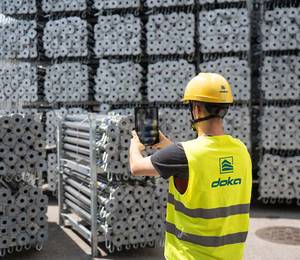