An Ammann ABC 180 ValueTec asphalt plant has been used on a recent project at the Chhatrapati Shivaji Maharaj International Airport in Mumbai, India. The work included resurfacing and profile correction of runway intersections, which took place between 7 February and 30 March 2019.
The job was quite challenging. An average of 1,000 flights arrive or depart from the airport every day. To minimise disruptions to service, the airport was closed daily for only six hours. Even this limited timeframe impacted approximately 240 flights during each closure. Plant production and dependability were crucial to meeting the project deadline.
AIC Infrastructure handled the asphalt production and placement. The company utilised the Ammann ABC 180 ValueTec plant, which produced approximately 700 t of asphalt mix per day to help keep the resurfacing work on track. The company also deployed two Ammann AP 240 pneumatic tyred rollers, two ARX 91 tandem rollers, and an AFT 600-3 tracked paver.
According to AIC Infrastructure, the biggest challenges were “procurement of plant and machines, time management to ensure everything was executed as planned, quality to meet the desired parameters, and safety to ensure zero incidents and zero accidents.” In the end, the project was completed successfully – on schedule, with minimal interruptions to travellers.
Kritharth Raja Desai, managing director of AIC Infrastructure, reported that the Ammann plant, paver and rollers were the ideal solutions for the project. “Excellent team work, a pro-active approach and the customer centricity of the Ammann team members helped us to complete the runway resurfacing and profile correction work at India’s busiest airport within the stipulated timeframe,” he said. “We are happy to note, we did not lose even a minute of productivity.”
Mr Desai added that several factors contributed to the successful project completion. “The Ammann customer support team was very cordial and cooperative in extending on-site parts support. In addition, Ammann India deployed trained operators and technicians on-site, which helped us become productive instantly.”
Ammann engineers monitored the condition of the plant and machines nearly every day. Proactive maintenance ensured there were no breakdowns. “The best part is, the maintenance routines were scheduled by Ammann India in such a way that our productive hours were not impacted at all,” said Mr Desai. “The suggestions given by Ammann India towards proactive maintenance were very helpful and gave our team a new perspective on how to achieve more with Ammann products.”
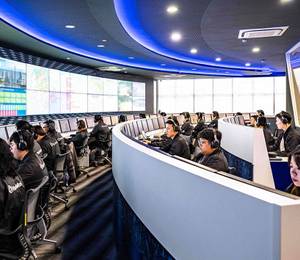
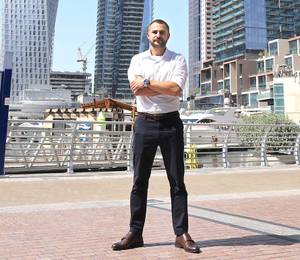
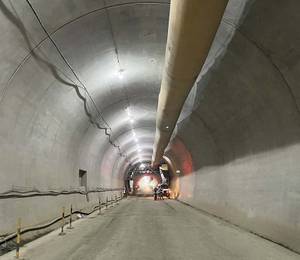
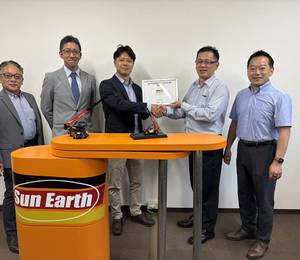

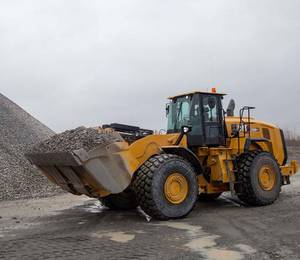

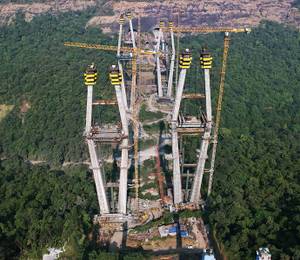
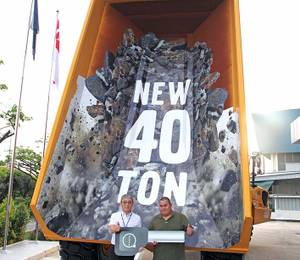
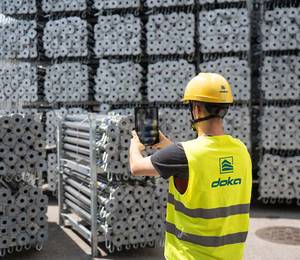