While the concrete industry continues to boost global infrastructure development, populations across the globe are also looking for greater sustainability and environmental care from the world around them. In the construction equipment segment, Lintec & Linnhoff has remained a pioneer in driving improved sustainability in construction materials supply, with a number of innovative designs aimed at boosting productivity while simultaneously limiting adverse environmental impact.
One example in Kuala Lumpur, Malaysia, saw a Eurotec MZP200 ready-mix concrete plant installed within an enclosed warehouse in the Chan Sow Lin district as part of a sustainability drive in 2014. According to Lintec & Linnhoff, this design idea proved so successful that other companies in the country adopted it, leading to significant improvements in local air quality.
“Seven years ago, this was the only plant in Malaysia with the enclosed design, but it quickly caught the attention of the local construction industry who were all impressed with the reductions in noise and dust emission levels it delivered,” said R. Sakthi, CEO of Lintec & Linnhoff Concrete Pte Ltd. “This greatly improved air quality and helped the Malaysian industry take another step towards more sustainable infrastructure development.”
Similar to the other ready-mix concrete plants in the MZ series, the Eurotec MZP200 features a modularised structure for easy and quick installation and maintenance. The project in Chan Sow Lin was completed inside an almost totally enclosed warehouse, with the plant’s six aggregate bins, multiple tall cement silos, centre-discharge conveying system and static aggregate ground-feeding conveying system all assembled within the giant structure, shared Lintec & Linnhoff. This way dust and cement were contained within the compound, rather than polluting the external environment and nearby residential areas.
Production volume up, audible volume down
The Eurotec MZP200 worked for 10 hours per day, producing up to 4.5 cu m per batch or up to 200 cu m/hr of ready-mix concrete for construction and infrastructure projects in Kuala Lumpur and the Klang Valley. Despite this, the plant was notable for the reduced noise and dust.
By March 2015, the Eurotec MZP200 achieved another milestone when it was awarded SIRIM QAS International Sdn Bhd’s ISO 14001:2004 certification in the Manufacturing of Ready Mix Concrete category.
“Our engineering detail allows the MZ batching plant model to fully reclaim returned concrete by separating the sand, aggregates and water, and then recycle them back into the batching process,” said Mr Sakthi.
The combination of an enclosed warehouse for the concrete plant, plus an operational capacity to fully reclaim returned concrete is a perfect design for urban locations. “Increasingly in Asia there is greater attention being paid to delivering better air quality, with the Asian Development Bank even launching a Clean Air for Livable Cities series to support the initiative,” explained Lintec & Linnhoff.
“At the same time, demand for greener construction continues to rise, and interestingly this is being supported by end users, with recent research showing that most Asia Pacific companies would pay higher rent to lease a building with stronger green credentials.”
The manufacturer added that as this trend continues, contractors will increasingly look for innovative designs and advanced technology in their mission of producing good quality concrete that can help them deliver more sustainability-certified buildings.
Customisable design to suit local needs
With an extensive range of customisation options to suit the requirements of any major project, the Eurotec MZ series can be designed with one mixer and two discharge chutes to reduce the waiting time of mixer trucks, thereby increasing productivity and reducing fuel use. The energy consumption – along with wear and maintenance costs – of the plant is also reduced via the use of computer-controlled twin-shaft mixers that ensure high accuracy. Operating at high torque, their three-dimensional mixing motions generate a higher consistency of concrete.
“This project showed that it is entirely possible for concrete batching plants and local residents to co-exist peacefully, as long as proper attention in detail is paid to the environmental impact,” concluded Mr Sakthi. “Now the enclosed ready-mix concrete plant has become popular and other jobsites have started adopting it to reduce pollution. This is one early design innovation we are rightly proud of, but we have lots more coming in the future too!”
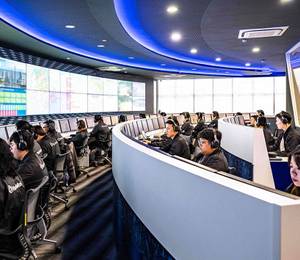
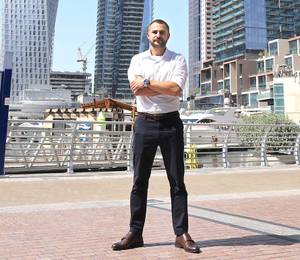
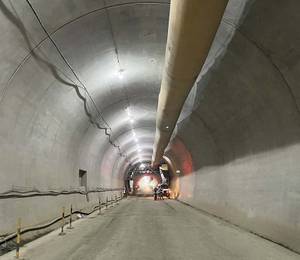
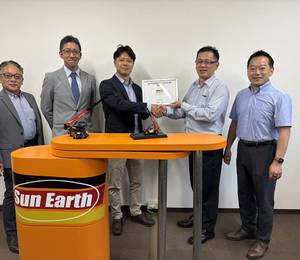

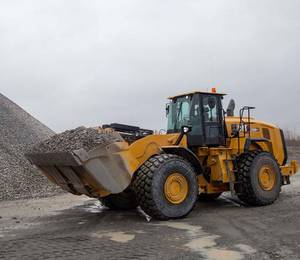

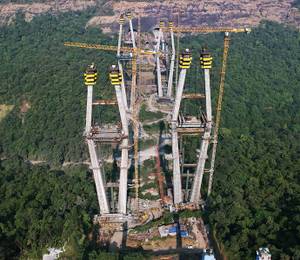
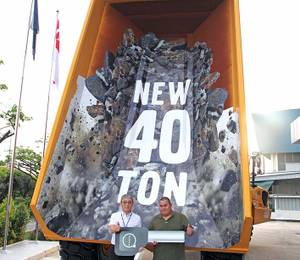
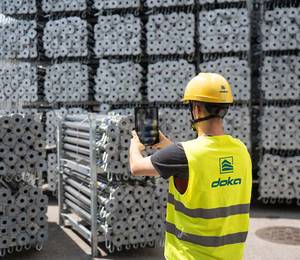