Rubble Master (RM) has introduced a new fleet management and condition monitoring system, called RM XSMART. Developed in-house, this digital technology combines satellite-based location tracking and advanced telemetry with cloud-based software packages and mobile apps for the best possible connectivity.
“When I founded RM 30 years ago, I never imagined that one day the RM team would file a patent to do with artificial intelligence and digitalisation,” said RM founder and CEO Gerald Hanisch. “For us it’s important to keep a 360° view. We take a look at everything directly on-site together with the customer to find potentials for how we can drive the construction site of the future.”
RM XSMART is the abbreviation for NeXt Level Site Management by Advanced Remote Technology. The system features fleet management and condition monitoring in one tool as the next stage in the development of RM GO! SMART.
According to RM, while operators can still display all data and troubleshooting routines directly on their smartphones at any time, in the future the data will not only be available in the machine’s WiFi network, but anytime and anywhere. This makes the daily work of workshop managers, rental fleet managers, dispatchers and owners much easier.
“We don’t want our customers to waste time doing paperwork for their machines. Our aim is to offer the best service and that includes making the maximum profit,” said Mr Hanisch. This is achieved by centralising and automating the flow of information. RM XSMART gives detailed records relating to operating data as well as operating times.
With just a few clicks, the data from RM XSMART can be broken down to the exact day and time. RM highlighted that since the operating hours are recorded automatically, it is no longer necessary to log hours at regular intervals manually. These records replace handwritten logbooks for each machine and are available at any time as a PDF download for presentation to the authorities.
Waiting times are reduced because diesel and AdBlue levels are recorded continuously, and thus tankers can be dispatched in good time without the machine operator having to call. A frequent problem on construction sites – fuel theft – can also be detected at an early stage, added RM.
By using RM XSMART, the machine owner and dispatcher will have an overview of which machines are available, which are currently being serviced and which are already in operation, explained RM. Tags and notes can be used to pass on additional information, so that users always have a comprehensive overview.
RM XSMART also eliminates the time-consuming search for the exact location of a machine by service technicians or transport drivers. RM pointed out that regardless of whether the machine location has an exact postal address or not, the coordinates are noted in the system and can be shared at any time. In addition, the nearest postal address is provided for easier navigation.
“RM XSMART takes us another step towards the construction site of the future, but much more is still to be implemented, because the potential of the combination of electrification and digitalisation is enormous. That is why RM XSMART will be included with all ‘Next’ machines in the future, and the platform is available as an option on all GO! machines,” revealed Mr Hanisch.
Energy supply
“Because we take the entire processing chain into consideration, power management and networking each machine has emerged as a particularly important topic for us,” added RM chief technology officer Markus Gaggl.
Mr Gaggl believes the construction site of the future is electric. “The automotive industry is setting the pace here. Considering that the decision has been made to practically phase out combustion engines by 2030, there will be many more electric construction machines in the foreseeable future.”
RM currently offers its customers the possibility to either connect to the grid or to work completely self-sufficiently. The company can also supply an entire processing line consisting of pre-screen, crusher and post-screen from a single power source. “These machines need to be able to communicate with each other to avoid belts running idle and to save energy,” said Mr Gaggl.
While autonomous crushers and screens are still in the development stage, RM already provides its customers with assistance systems in the form of Performance Indicator and RM XSMART to optimally feed crushers and screens.
“Construction sites will still vary greatly in the future,” explained Mr Hanisch. “Of course, it will be extremely important in urban areas that noise, emissions and dust are kept to a minimum. For construction sites in remote areas such as the jungles of Southeast Asia or desert regions in Central and South America, on the other hand, issues such as energy supply and predictive maintenance are key. That’s why our top priority is to respond flexibly.”
All images: Rubble Master
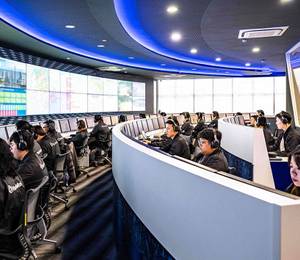
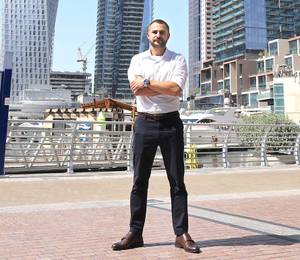
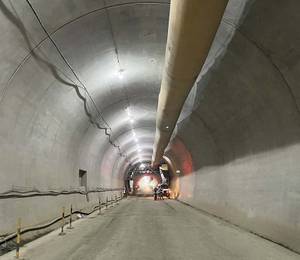
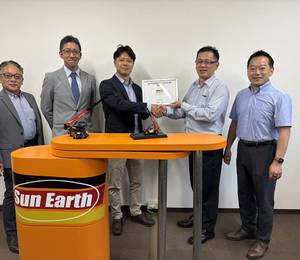

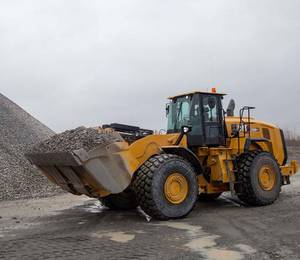

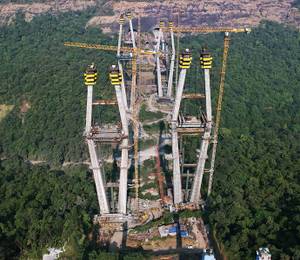
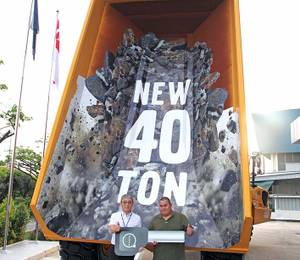
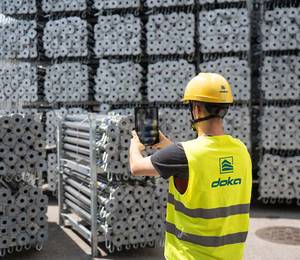