On display at bauma will be an Ammann burner, mixer, screen, the weighing and mixing level of an Ammann ABP HRT (high recycling technology) plant; and scale models of several plants. Demos of the as1 control system will also be available.
Ammann offers a variety of plant after-sales services, which can be explored as well. These include the use of augmented reality during plant maintenance and even installation.
The RAH100 recycling system is capable of producing mix up to 100% recycled materials. Ammann said the system’s gentle heating process results in excellent quality of recycled mix.
Additional systems from Ammann include the RAH50 and RAH60 dryers, which have maximum usage of 50% and 60% RAP, respectively. The RAC system maxes out at 40% usage.
According to Ammann, all of its recycling systems are able to produce high-quality mix with 100% virgin aggregate if so desired.
The use of alternative fuels is another highlight. Ammann utilises renewable energy sources or, in some cases, converts a waste product into fuel. This conserves natural resources and puts less pressure on landfills.
On the renewable front, a burner transforms wood dust – a material that is available from local sources – into fuel. The carbon dioxide released when burning wood is offset by the fact the tree consumed that amount of carbon dioxide during its life. Therefore, the emissions are carbon neutral.
The burner has proven effective and is utilised on a number of plants, said Ammann. It can be retrofitted as well.
In addition, Ammann biofuel burners can utilise more traditional fuels such as natural gas, LPG, light and heavy oil and kerosene. This alleviates the concerns of customers who are hesitant to rely solely on newer fuels.
Ammann also offers varied sound-suppression packages to meet customers’ needs. The efforts start with equipping burners with variable speed motor drives, which are much quieter, and stack silencers, which control exhaust noise. The company provides more and more sound-suppression options, all the way to cladding the entire plant.
Retrofits are a way to improve sustainability with existing plants, and to enhance productivity, added Ammann. Regulations are frequently updated for noise and dust emissions, sampling options, the production of foamed asphalt and the feeding of additives into mix.
Retrofitting, centred on improving an existing plant to meet the same standards as its newer counterparts, is a much more cost-effective approach. Ammann’s retrofitting process is available for its own asphalt-mixing products and those of other manufacturers.
Bauma booth: FS.909
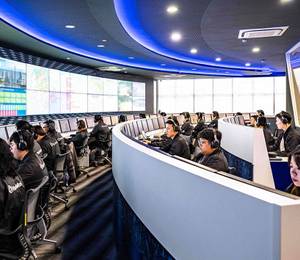
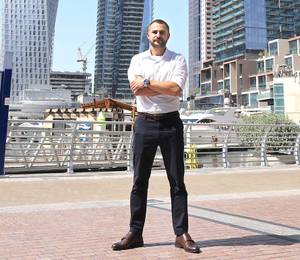
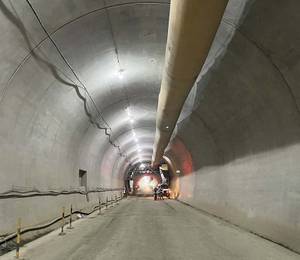
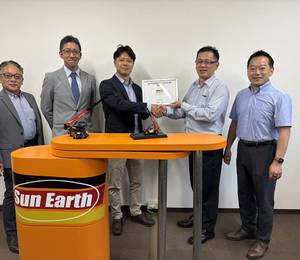

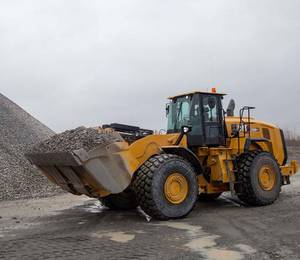

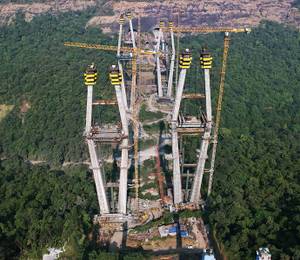
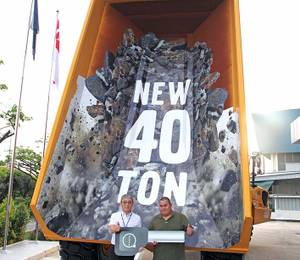
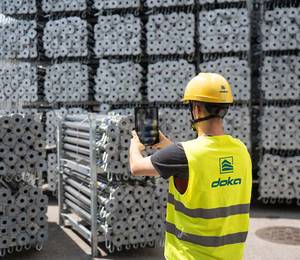