The refreshed Built Environment Industry Transformation Map (BE ITM) will help stakeholders within the sector collaborate more effectively across the value chain, said Desmond Lee, Singapore’s Minister for National Development and Minister-in-charge of Social Services Integration, at the opening of the International Built Environment Week (IBEW) 2022.
The Construction ITM and Real Estate (Facilities Management) ITM, previously launched as two separate ITMs in 2017 and 2018 respectively, have been amalgamated into one BE ITM to transform the sector through the three key stages of a building’s life cycle – from planning and design, construction, to operations and maintenance.
Planning and design phase
One of the key transformation areas is on integrated planning and design (IPD), where stronger collaboration across the building’s life cycle can optimise resources. This will build on the existing efforts for integrated digital delivery (IDD), which allows project stakeholders to collaborate with one another through digital platforms.
Design considerations for the building’s entire life cycle, including facilities management (FM), are factored in at the design stage, enabled by digitalisation, common data environment (CDE) standards and progressive procurement.
“We have worked with the industry to develop CDE data standards for all built environment stakeholders to adopt,” said Mr Lee. “We will drive the adoption of these standards through the new Corenet X platform, which we are currently working on.
“All BIM submissions for development projects via Corenet X will be required to comply with these standards. I spoke about Corenet X at IBEW last year, and you can look forward to the launch of this new system in the second half of next year.”
Under the refreshed BE ITM, the Building and Construction Authority (BCA) expects to increase the IDD adoption rate by gross floor area (GFA) for new developments from 34% today to 70% by 2025. The BE ITM also encourages the industry to move towards collaborative contracting where contracting parties, including the builder and facilities management firm, work together towards shared project goals at the start of the project.
According to BCA, seven government procuring agencies have identified nine upcoming projects to pilot collaborative contracting. Contract Management consultants such as Turner & Townsend, WT Partnership, AECOM and Threesixty are also supporting this effort by providing advisory services to private sector clients.
Construction phase
The second transformation is through advanced manufacturing and assembly (AMA), to enhance the efficiency of the supply chain and construction process by mainstreaming design for manufacturing and assembly (DfMA). This has helped firms reduce their reliance on foreign manpower and raise productivity.
Moving forward, BCA targets to increase the DfMA adoption rate by GFA from 44% today to 70% by 2025. Under AMA, more off-site production will be done in a factory environment with greater adoption of automation.
“Firms that have leveraged DfMA technologies, such as prefabricated prefinished volumetric construction (PPVC), have produced some good results,” noted Mr Lee. “Hence, we will continue to mainstream DfMA as the default method of construction.”
By improving the quality of work and working environments, including at the construction site, the industry hopes to attract and retain talent in the sector, said BCA. The shift from a project-based building approach to a modular, product-based one also enables industry firms to reap greater economies of scale.
“We aim to be less reliant on low-skill foreign manpower and really go upskill and up the value chain in construction technology. Our latest move is to require all large building projects to adopt DfMA technologies from April this year,” explained Mr Lee.
“We will also continue to support [the industry] in this DfMA journey. For instance, we recently extended the Productivity Innovation Project (PIP) scheme, which co-funds up to 70% of the cost premium of DfMA technologies. This includes funding for equipment and systems required in integrated construction prefabrication hubs, or ICPHs. Firms can continue applying for support under PIP until March 2024.”
He added that the industry “can do more to maximise the benefits of shifting construction activities to off-site, factory-like settings. For example, we can incorporate more automation and robotics into the production of precast and PPVC modules, to deliver greater manpower savings and achieve even higher productivity.”
At the same time, BCA is also working with stakeholders to establish new integrated construction parks (ICPs) across Singapore. In ICPs, construction facilities such as aggregate terminals, aggregate storage yards, ready-mix concrete (RMC) batching plants and precast plants will be co-located for greater synergy across the entire supply chain.
The ICPs will provide a platform for firms to develop their DfMA solutions and production facilities. Synergistic construction supply chain activities will be co-located within the park to streamline logistics. ICPs will also leverage advanced technology to make production more productive, greener and cleaner.
The first ICP at Jurong Port is scheduled to progressively begin its operations from December 2022. “We will be trialling the ICP concept at Jurong Port before looking into how this concept can be further replicated in other locations,” said Mr Lee.
“By bringing these facilities closer together, co-locating them together, we can achieve greater efficiencies in producing construction components. For instance, raw materials like cement, sand and granite can be transported to the RMC batching plants using mechanised conveyor systems, rather than hauling them across the island in lots of vehicles.
“Production facilities such as ICPHs will be allocated a longer tenure than typical traditional yards, so that the operators can invest in advanced technologies to operate in a much more productive manner.”
Operations and maintenance phase
The third key transformation area, sustainable urban systems (SUS), will facilitate the ramping up of decarbonisation efforts in the industry for a more sustainable and liveable built environment. SUS aims to achieve low-emissions buildings and districts with efficient building management enabled by Integrated, Aggregated and Smart FM.
Under SUS, BCA will continue with existing efforts to meet its ‘80-80-80 in 2030’ targets set under the latest edition of the Singapore Green Building Masterplan. BCA will also aim for a more ambitious target of 80% of public buildings adopting Smart FM by 2030, and set a new target for 40% of private buildings by GFA to adopt Smart FM by 2030.
Announced earlier this year, the S$30 million Integrated Facilities Management (IFM) and Aggregated Facilities Management (AFM) Grant for firms which wish to adopt IFM/AFM will be open for applications from 6 September 2022. BCA said about 10 companies have expressed interest in applying for the grant so far.
BCA further highlighted that, as Singapore embarks on the BE ITM, there is also a need to adopt a more ambitious approach in transforming the value chain as a whole, and push for best-in-class outcomes in projects. Developers and sector leaders are beginning to recognise the pivotal role they play in transforming the industry by running and developing a capable supply chain.
To this end, BCA has been developing the Growth and Transformation Scheme (GTS) to pilot this value chain approach. A set of outcomes for the GTS has been developed with inputs from the industry over the past year to support these strategic alliances.
Lastly, in recognition of projects that have embodied the transformation goals of the ITM, the newly launched Built Environment Transformation Award recognises firms and industry practitioners who have honed their capabilities to build projects that exemplify productivity, digitalisation and sustainability. This year’s winners include The Tapestry, PSA Liveable City, Eunoia Junior College as well as JTC’s 1 and 7 North Coast developments in Woodlands North Coast.
Image credits:
Images 1-2: Jurong Port
Images 3-4: BCA
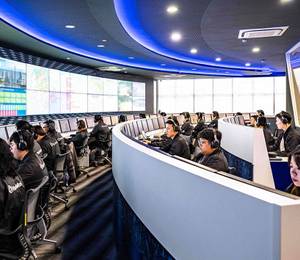
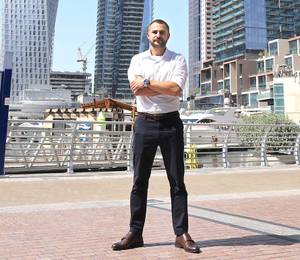
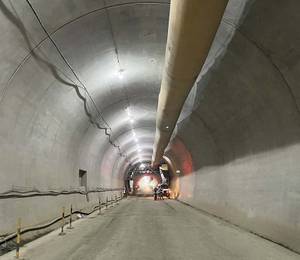
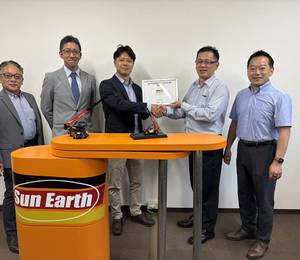

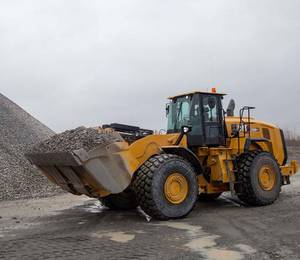

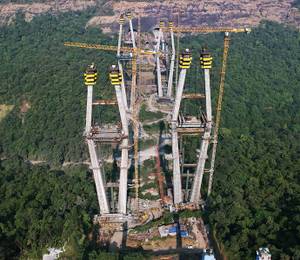
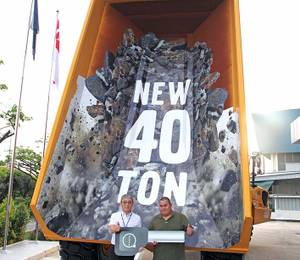
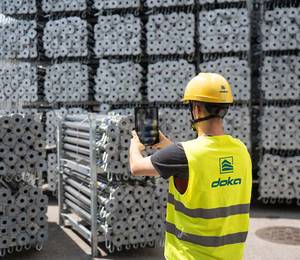