Singapore’s Housing & Development Board (HDB) has announced that it will accelerate its push towards higher construction productivity in public housing projects, setting a new target of 40% site improvement by 2030.
In 2020, HDB achieved a 25.9% productivity improvement, exceeding the target set in 2010 to achieve a 25% improvement by 2020. Since 2021, the adoption of design for manufacturing and assembly (DfMA) in all new HDB projects, as well as integrated digital delivery (IDD) in some projects, has continued to contribute to productivity growth.
A key initiative in meeting HDB’s new target is a Construction Transformation Project (CTP), which will pilot a range of innovations and technologies to further raise productivity. In partnership with construction firm Obayashi Singapore Pte Ltd, HDB will adopt the latest advanced construction technologies to design and build the upcoming ‘Garden Waterfront I & II @ Tengah’ build-to-order (BTO) project. When completed, this CTP aims to realise a 25% improvement in productivity as compared to other BTO projects then.
“The pandemic over the past two years posed tremendous challenges to the building industry, not least in terms of workers shortage and supply chain resilience. As the largest housing developer in Singapore, HDB is keenly aware of our role as a catalyst and market mover in driving construction productivity and transformation of the built environment sector,” said Tan Meng Dui, CEO of HDB. “Our efforts in harnessing technology, including DfMA and IDD, have enabled us to continually improve productivity over more than two decades, and this continued even in 2021 when productivity improvements reached 26.2%.
“With the CTP, we hope to raise the bar further and find novel ways to construct quality homes with less manpower, faster and safer. These efforts, which are geared towards achieving construction productivity improvements of 40% goal by 2030, will also enhance the resilience of our construction ecosystem, and support the ramp-up of HDB’s building programme over the next few years and deliver HDB flats faster to our buyers.”
Construction Transformation Project
For the Garden Waterfront I & II @ Tengah development, HDB will adopt new technologies and innovations in the design, fabrication and construction stages. Key takeaways from this project will be studied for future implementation in other BTO projects.
HDB will use virtual design and construction (VDC) to simulate the design and construction activities virtually, so that they can be refined further by consultants and contractors before the actual construction on site. This allows greater integration and collaboration among stakeholders across the construction value chain.
One main component of VDC is the virtual mock-up unit, a digital twin of the actual residential unit with a high level of detail such as the positions of pipes, sanitary fixtures, power points, switches and furniture. This gives the project team an ‘X-ray vision’ of the unit, enabling the team to identify and resolve potential design and construction issues upstream collaboratively.
Previously, life-size physical mock-ups of the kitchen and toilet using plywood (timber mock-ups) had to be built, and this took up more time, effort and resources. All new HDB projects launched from 2022, including the CTP, will use virtual mock-ups instead of timber mock-ups.
HDB will also use a hybrid precast system – incorporating both 2D and 3D precast components – for the residential units in this CTP. Currently, full 3D prefabricated prefinished volumetric construction (PPVC) components are used in many HDB projects.
The more efficient, hybrid precast system will enable HDB to design and build residential units using a beamless flat plate system. This results in consistently higher headroom compared to flats in typical BTO projects which have beams. As such, residents will have greater flexibility in configuring the layout of their flat.
At the same time, HDB is piloting the use of 3D concrete printing for small streetscape furniture and other landscape features for some projects in Tengah and Bidadari. For the CTP, HDB will go one step further to use a special fibre-glass reinforced concrete material to provide structural strength. This innovations allows HDB to potentially use less material than conventional 3D printing methods, and also paves the way for studies on larger and more complex structures to be potentially fabricated in this manner without the need for complex moulds.
In addition, to allow for cleaner, higher quality and less manpower-intensive construction, HDB will be testing a few innovations from Obayashi on a pilot basis, to study their impact on productivity and construction safety.
To reduce manpower required for repetitive and labour-intensive activities such as operating tower cranes, HDB will use artificial intelligence (AI) in tower crane operations to optimise the hoisting routes for precast components. The light detection and ranging (LiDAR) technology is also used to detect and avoid collisions.
Likewise, crawler cranes are still largely operated manually. With the crane machine guidance technology, crawler crane operators will be guided on the optimum path for lifting the elements in the construction of the multi-storey car park, using a combination of LiDAR and building information modelling (BIM).
In place of workers to guide the components into place or to make manual adjustments using guide wires, the SkyJuster – which is attached to the end of the hoisting block – will orientate precast elements to their correct position before they are lowered into place. This helps to reduce the number of workers needed for the precast installation process.
HDB will also adopt IDD for the project. Digital technologies will be deployed extensively to integrate work processes and connect stakeholders throughout the various stages of the construction and building life cycle, through a cloud-based common data environment. For example, precast components will be automatically tracked using RFID or Bluetooth tags from the time they are fabricated at precast yards, to when they are delivered to site and assembled. IDD helps to better manage the logistic planning and management of precast components from the precast yard to the construction site for the project.
The innovations in this CTP are expected to yield higher productivity through more efficient use of manpower and resources, while reducing material wastage. Together with the adoption of digital technologies for tighter and more effective collaboration between project stakeholders, from design to construction, HDB targets to achieve a 25% improvement in productivity compared to other BTO projects.
Collaborations with various stakeholders
Beyond the CTP, HDB also partners researchers, Institutes of Higher Learning (IHLs) and companies to continually explore ways to address challenges related to construction productivity and sustainability. Two key initiatives are the Cities of Tomorrow R&D programme and the Cool Ideas Enterprise platform.
The Cities of Tomorrow (CoT) R&D programme aims to establish Singapore as a highly liveable, sustainable and resilient city of the future, and a vibrant urban solutions hub. HDB, along with the Ministry of National Development (MND) and the Building and Construction Authority (BCA), will be launching new grant calls soon in search of innovative solutions in the areas of advanced construction productivity, infrastructure resilience and facilities management.
These will include the development of solutions to: develop infrastructure to enable robotic assembly on construction sites; automate inspection, diagnose and maintain external building facades; geo-reference and detect underground services and assets for new estates; and automate the collection of waste at older estates served by individual refuse chutes.
Furthermore, HDB and Enterprise Singapore have committed another S$5 million to support the Cool Ideas Enterprise (CIE). The additional funding provided to the open-innovation platform will continue to support enterprises’ efforts to co-develop solutions to improve HDB living. To this end, HDB is currently calling for solutions to increase productivity and reduce manpower at construction sites and off-site facilities (e.g. precast yards) through automation or digital solutions, without compromising quality and safety. Interested parties can visit HDB InfoWEB for more details.
Image credits:
Images 1-3: HDB
Images 4-5: Obayashi Corporation
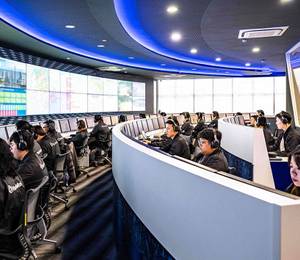
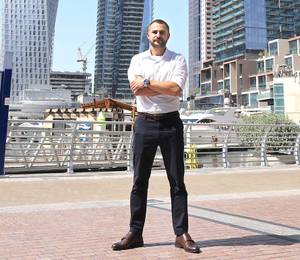
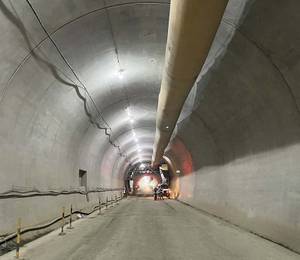
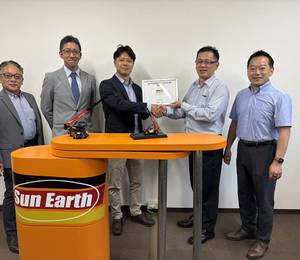

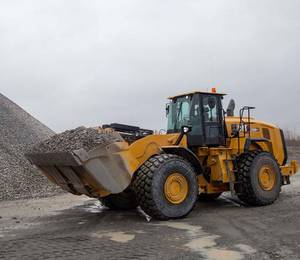

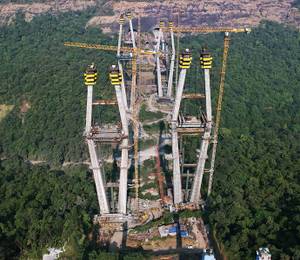
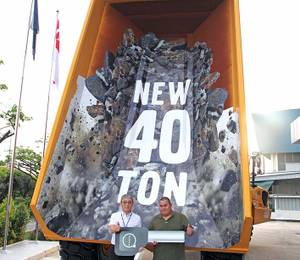
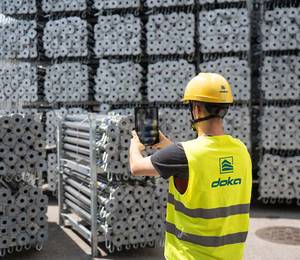