Situated in the east of Ezhou in Hubei province, the new Ezhou Huahu Airport has been developed as an international airport, multimodal cargo hub, and aviation logistics port, and serves as a gateway for air trade between China and the rest of the world.
The airport is China’s first professional airport cargo hub, which includes a passenger terminal and one of the world’s largest transfer centres. It is expected to function not only as a freight hub, but also as a passenger transport branch line, public platform, and aviation base.
The CNY 30.8 billion project covers 11.89 sq km and a total construction area of 900,000 sq m. As one of the largest air cargo hubs in Asia, it provides facilities for widebody aircraft and is designed to handle 2.45 mil t of cargo and 1.5 million passengers per year by 2030, increasing to 9.08 mil t of cargo and 20 million passengers annually by 2050.
Connecting with provincial railway, waterway, expressway, and air transportation infrastructure, this completed integral airport covers five national-level city clusters, benefitting 90% of the country’s economic output and 80% of its population. Hubei International Logistics Airport is responsible for overall airport construction and operation management.
Multiple participants, voluminous data, and complex processes
The sheer size and scale of the project presented coordination and technical challenges, compounded by complex geological conditions and a tight schedule. The airport’s transfer centre alone spans a construction area of 750,000 sq m, covering a floor space of 300,000 sq m, and is one of the largest trans-shipment centres in the world. Comprised of three major areas – a flight area, terminal, and transportation system leading into and out of the airport – the facility includes numerous complex equipment processes, requiring modelling and integration, and involves coordinating civil aviation, municipal administration, and construction works.
With three different industries, 29 disciplines consisting of more than 50 parties across various locations, and over 600 on-site personnel, the project was difficult to manage and coordinate. Therefore, it required a collaborative digital environment to streamline workflows and keep the project on schedule. Hubei International Logistics Airport wanted to implement a comprehensive BIM methodology and digitalise the planning, design, construction, management, and operations processes. However, faced without an existing civil aviation BIM standards and tens of millions of model components, the team realised that it needed an integrated digital technology solution capable of supporting large volumes of multisourced data and intelligent lifecycle operations.
“The Ezhou Huahu Airport has 25 million model components, the largest number of required model components recognised in the domestic BIM field. The project needs a suitable platform to carry large volumes of data and view BIM attributes, while also ensuring the smooth operation of the model,” explained Zou Xianqiang, chief engineer at Hubei International Logistics Airport.
Leveraging BIM and iTwin technology
Hubei International Logistics Airport deployed several innovative solutions to help overcome the challenges on this project. For example, it selected Bentley’s BIM and the Bentley iTwin platform to handle a massive amount of data, coordinate among the multiple project participants, and deliver a high-precision model that could be applied to manage on-site construction and facility operations. Additionally, the team used ProjectWise to establish a collaborative digital work environment, which helped streamline workflows among the various disciplines and more than 50 participating units engaged in on-site BIM work.
Using Bentley’s modelling applications, Hubei International Logistics Airport developed a 3D model of the airport and the first BIM-based, full-lifecycle digital construction management platform in China’s civil aviation industry. Lastly, with OpenRoads, the team could develop a rapid professional modelling tool containing 11 categories and 40 sub-items, and a database that includes over 30,000 component types. The benefits of using the software enabled Hubei International Logistics Airport to build the underground pipeline network and create a pavement compression model for rapid partitioning of concrete pavement in the flight area. “250,000 pavement slabs were partitioned in one click, which ensured on-site construction accuracy,” said Mr Xianqiang. Moreover, integrating ProStructures and Navigator helped coordinate structural modelling with the on-site construction team, utilising mobile devices.
Based on the Bentley iTwin platform, Hubei International Logistics Airport integrated 25 million model components from the different BIM applications, generating a cloud-based digital twin capable of incorporating the voluminous engineering data and model elements, supporting construction management and lifecycle operations.
“The Ezhou Huahu Airport makes full use of iTwin technology, independently researches and develops an innovative application platform, and combines the BIM model to integrate the airport’s all-discipline model, as well as enable the BIM data management of the airport project,” stated Mr Xianqiang. Using Bentley’s integrated BIM and iTwin technology facilitated construction of the digital airport, enabling the creation of a high-precision 3D model and digital twin to optimise multidiscipline design, construction, and overall project management.
Digital twin drives smart industry practices
Working in an open connected data environment using Bentley’s BIM applications and ProjectWise helped Hubei International Logistics Airport streamline multidiscipline collaboration across all three industries, shortening model delivery time by 90 days and saving CNY 12 million. Compared to traditional construction methods, using Navigator to provide and engage the on-site construction team with the model improved productivity by 25%. Bentley’s iTwin technology provided a cloud-based platform, featuring large modelling capacity to develop a digital twin supporting voluminous, multisourced 3D data, models, attributes, and documents.
By introducing the concept of digital twins, Hubei International Logistics Airport established a comprehensive digital context for the entire project, enabling the team to pinpoint design changes in advance and avoid changes during construction, which greatly reduced costs and shortened the construction period. “Through whole-process digital management, the digital quality in design construction was effectively guaranteed and [we saved more than 200 days during] the construction period,” shared Mr Xianqiang. The digital twin solution resolved approximately 6,000 issues and realised zero demolition on site, saving CNY 300 million in project costs.
In addition to solving technological and coordination problems, the team used Bentley applications to develop China’s first BIM components information table, covering BIM standards for 29 professional systems across three industries of civil aviation, construction, and municipal administration, which gave Hubei International Logistics Airport a foundation to construct a digital airport. Through the practice and application of iTwin technology and digital twins, the team implemented innovative digital management concepts and workflow process to achieve full lifecycle BIM application and intelligent practices for China’s civil aviation industry.
“[The project] provides a valuable reference for BIM application in the digital construction of [a] civil aviation airport, accelerating construction of smart civil aviation and building an industrial ecology that promotes the construction of smart civil aviation in China,” concluded Mr Xianqiang.
All images: Hubei International Logistics Airport Co Ltd / Shenzhen SF Taisen Holdings (Group) Co Ltd / Airport Construction Engineering Co Ltd
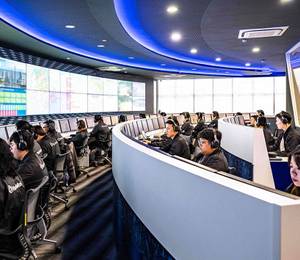
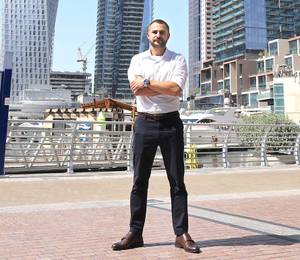
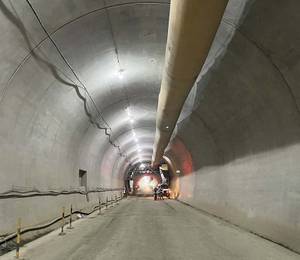
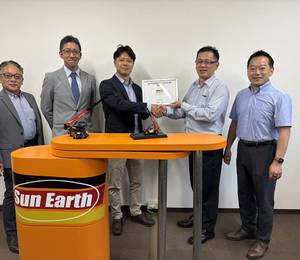

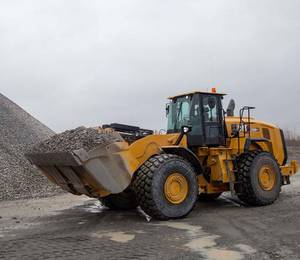

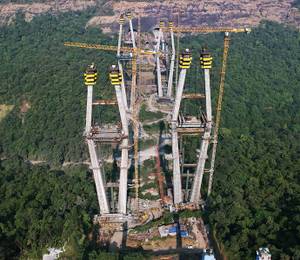
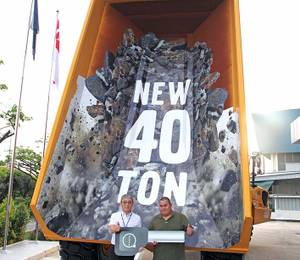
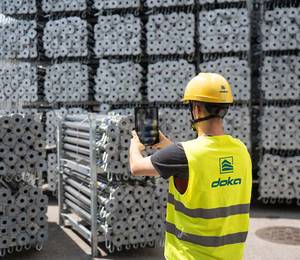