Construction work on the Ningpan-Panzhihua Expressway in China is currently underway. To deliver the project effectively and accurately, the contractor on the job opted for a combination of the Vögele Super 3000-3i paver, Hamm HC 228 D compactor and Hamm HD 0128V tandem roller from the Wirtgen Group.
As the foundation of the road, the base course is a crucial element – it improves the load distribution and therefore increases the longevity of the asphalt surface course. Compaction plays a key role in this, ensuring that the road surface is sufficiently stable and durable to withstand a constant flow of traffic and the effects of natural forces.
The first step was to pave the ballast base course using the Vögele Super 3000-3i. This versatile machine is ideal for constructing ballast base courses with large layer thicknesses. The first layer on the 26-m-wide carriageway of the Ningpan Expressway was paved as two lanes, each measuring 13 m, at a speed of 4 m/min and with a paving thickness of 18 cm.
“The fuel consumption is around 10 l/hr with low vibration and around 13 l/hr with strong vibration for uninterrupted work. That’s extremely economical!” said the machine operator.
The contractor deployed different rollers when paving both the ballast base course and the hydraulically bound base course. However, the high compaction quality was primarily achieved with the Hamm HC 228 D compactor, revealed Wirtgen. The evenness of the carriageway was significantly improved. This meant that, even on the day of the first measurement and three days later for the subsequent measurement, ≥96% of the required compaction values were met. What’s more, for the hydraulically bound base course, this figure was as high as ≥97%. After the total compaction was completed, the degree of compaction of both layers, which were 36 cm thick in total, only showed a deviation of 0.3%.
High-performance machines with innovative systems
The Vögele Super 3000-3i is the largest paver in the range and designed for paving widths of up to 18 m. Wirtgen said the entire width of the road can be paved in a single working gear. This high continuous operation is made possible by a high-performance Cummins engine with a maximum power of 354 kW and a paving capacity of 1,800 t/hr.
The innovative material conveying concept enables a high conveying capacity, an excellent material flow and an optimal distribution of mixed material for different layers. A special feature of the Super 3000-3i is that the height of the rear part of the chassis, including the conveyor belt and spreading auger, can be continuously adjusted at the touch of a button. So the material is always transferred onto the spreading auger from above, which is an ideal discharge point.
Another highlight of the Super 3000-3i is the option of hydraulically adjusting the tamper stroke for varying layer thicknesses. All it takes is the touch of a button – this speeds up the work process and ensures high-quality compaction results.
Meanwhile, the HC 228 D belongs to the next generation of fully hydraulic compactors from Hamm. Its weight of 22 t is well distributed between the front and rear wheels, thus giving the compactor a higher compaction power than comparable machines in this weight class and playing a key role in achieving the required compaction value, said Wirtgen.
In addition, the HC 228 D is equipped with the intelligent Hammtronic machine management system. Among other functions, the system enables the compaction speed to be pre-set with precision and prevents bulge formation thanks to smooth acceleration and braking. According to Wirtgen, measurements taken at different points in the new road have shown that the degree of compaction only varies by 1% – an evidence that the new functions significantly improve the compaction quality.
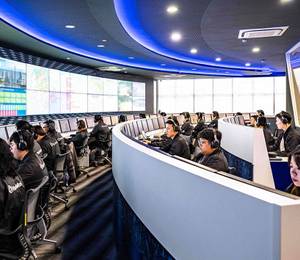
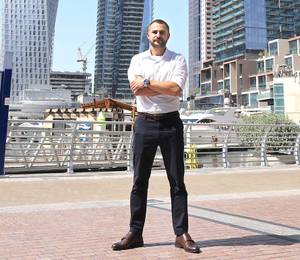
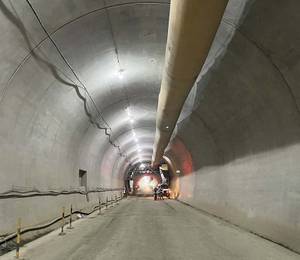
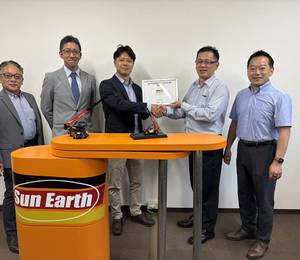

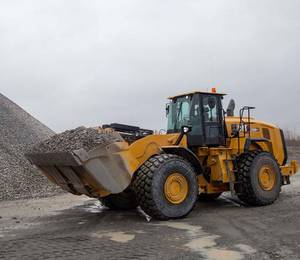

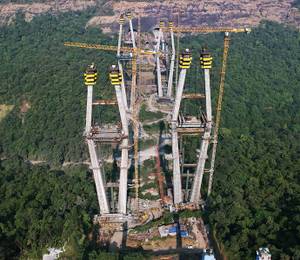
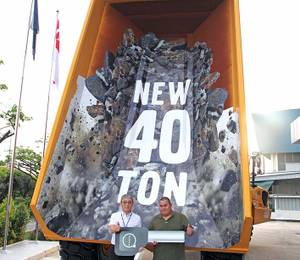
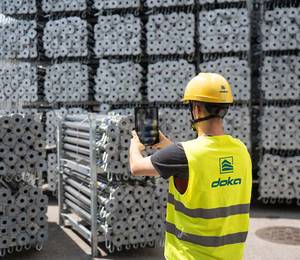