Tadano’s new AC 5.250-2 was unveiled at bauma 2022. As part of the final stretch of development for the crane’s launch, the company has now outfitted the machine with additional features, particularly in the area of safety.
This five-axle all-terrain crane offers a maximum capacity of 250 t. It has a main boom length of 70 m, which can be extended by 42 m with an HAV main boom extension, allowing it to reach a system length of 112 m. According to Tadano, all available main boom extensions from 5.8 to 36 m are self-rigging.
The AC 5.250-2 features a lifting capacity of 14.5 t with a 70-m boom length at a radius of 12 to 24 m, and a lifting capacity of 11 t with a boom length of 47 m at a radius of 42 m.
A number of transportation configuration options are available for the AC 5.250-2. For instance, the crane can carry a three-sheave hook block for lifting loads of up to 67.3 t or a 5.8-m heavy-lift runner on board while remaining within a 12-t axle load configuration – not to mention that the transportation mounts for the HAV extension are included by default in the 12-t axle load.
Tadano said the AC 5.250-2 can be used as a taxi crane without a support vehicle while remaining within the legal axle load limit of 12 t. And if the axle load is increased to 16.5 t, it can also carry up to 20 t of its maximum counterweight of 80 t.
Key highlights
The AC 5.250-2 can pick up its total counterweight of 80 t in three lifts: 46.6 t with a full 360° radius of up to 6.2 m followed by two lifts of 15.2 t, with each split into 10 and 5.2 t for mounting on the right and left of the base package. If necessary, the counterweight can be split into smaller pieces as well, making it possible, for example, to pick up the 5.5-t base plate from a distance of up to 20.1 m across the full radius.
The IC 1 Plus control system determines the crane’s maximum lifting capacity for every boom position as a function of the superstructure’s slewing angle, and in real time to boot. Thus, the crane is always able to take advantage of the maximum lifting capacity available to it – especially during lifts over the outriggers. The outriggers can be extended asymmetrically to 0, 25, 50, 75, and 100% positions.
Using the Surround View camera system, the operators can optimally position the crane at work sites. This system uses six cameras to show a computer-assisted diagram of the maximum possible extension lengths for the outriggers at the crane’s current location.
The AC 5.250-2 is powered by a Mercedes-Benz engine with an output of 522 hp and a maximum torque of 2,600 Nm. The HVO-compatible diesel engine meets the latest EU Stage V requirements. It is also cost-effective thanks to the Eco Mode, which ensures that the engine always outputs the exact amount of power that the crane actually needs at any one time, with the IC-1 control system taking care of the corresponding calculations.
Furthermore, the spacious cab is designed for operator comfort. To ensure safety, there are intelligently positioned access points, attachment points for operators’ personal safety equipment, and a step that can be extended from the carrier to make it safe and comfortable to enter and exit the superstructure cab.
New safety features
Tadano has now incorporated its TailGuard active backup assist system to maximise safety during travel. This system uses two ultrasonic sensors to monitor the area behind the crane when backing up, and it works regardless of ambient light conditions. It shows the distance from stationary and moving objects in the monitoring area on the cab’s monitor, plays an acoustic warning before reaching obstacles, and will stop the crane itself in the event that there is a risk of collision.
The backup assist system is automatically activated the moment the crane’s reverse gear is engaged, so the process is very safe – it not only prevents injuries and property damage, but also crane downtimes associated with accidents.
In the future, the AC 5.250-2 will be fitted with another safety feature, Lift Adjuster, revealed Tadano. Scheduled to become available in the coming year, this solution consists of a technical control system that can be activated with the press of a button. It measures the boom’s deflection and independently adjusts the lift cylinder in order to compensate for the change in radius caused by the deflection and to eliminate the risk of swinging. This way, the Lift Adjuster significantly improves safety in the crane’s work environment.
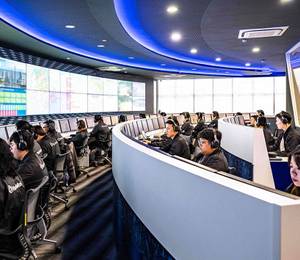
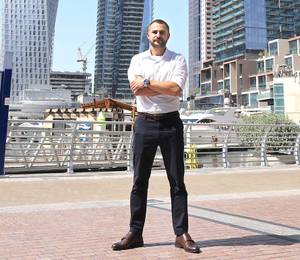
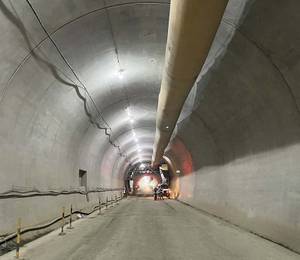
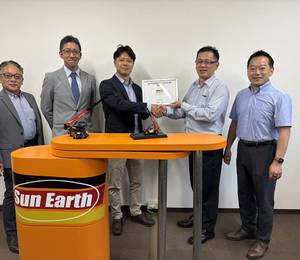

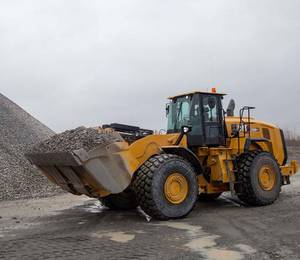

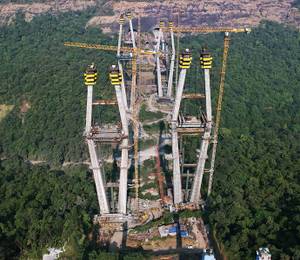
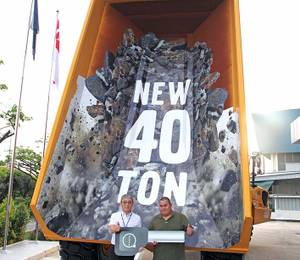
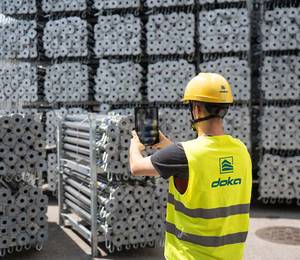