Liebherr has introduced a new carrier machine for slurry wall construction, the LBX 600, which is well suited for urban jobsites. Its compact size combined with the unplugged version enables work in highly confined spaces and noise-sensitive areas. The track width of its telescopic undercarriage can be reduced to 3 m, making it possible to transport the basic machine in one piece.
Featuring a modular system with three different booms, the LBX 600 can be flexibly equipped and customised to meet site requirements. The standard version of the machine has a total height of 17.8 m. For applications with restricted height, e.g. working under bridges, the Low Head with 11 m or Ultra Low Head with 5.8 m can be used.
Powerful grip
This new carrier machine is not only designed for work using a hydraulic grab but also with a mechanical grab or chisel, thanks to the two free-fall winches with a line pull of 300 kN each. In combination with the HSG 5-18 hydraulic slurry wall grab, the LBX 600 offers intuitive operation, which also enables hydraulic corrections to the grab alignment and thus a higher verticality of the trench.
The hydraulic slurry wall grab is modularly designed and has a robust base body. As the names of the grabs imply, HSG 5-18 C and HSG 5-18 L, slurry walls with thicknesses between 500 and 1,800 mm can be installed, depending on the composition. The term ‘C’ (compact) stands for the compact standard design for the Low Head version of the LBX 600, while the base body of the ‘L’ (large) version is 2.5 m longer. The resulting total height of the grab at 9.5 m and the high weight with low centre of gravity provide better vertical positioning and are especially advantageous when installing larger dimensioned slurry walls.
When working in difficult ground conditions, the execution of the work can be improved through increasing the dead weight of the grab with an additional weight of 4.4 t or 6.5 t. Bites with lengths of 2,500-3,400 mm and maximum depths of 80 m can be excavated with the grab.
Fitted with a hydraulic rotating device, the slurry wall grab can be aligned in all directions and provides quick and operator-friendly 180° rotation after each grab cycle. The high cylinder force of 1,527 kN achieves an excellent performance even under extreme conditions. The fill level indicator on the grab ensures high productivity throughout the entire application. The maximum permissible grab weight is 30 t.
‘Unplugged’
The LBX 600 is available in both conventional and battery-powered (‘unplugged’) versions, and they have identical performance data. One notable feature of the LBX 600 unplugged is that it delivers zero emissions; the machine does not produce any exhaust fumes and is extremely quiet.
The battery is charged using a conventional jobsite electric supply, and operation can continue as normal while charging. In order to change to battery operation, users just need to pull out the plug (hence unplugged). Whether attached to the electric supply or not, the performance and range of application remains unchanged. Liebherr offers the LBX 600 and LBX 600 unplugged as a complete package with the HSG 5-18 hydraulic slurry wall grab.
Digital solutions
All working processes for slurry wall construction can be electronically recorded and visualised using the process data recording system PDE. This system is operated and displayed on the PDE touchscreen in the cabin. PDE records operating data from the Litronic control system, as well as data from external sensors.
Using the MyJobsite software solution, all relevant process, machine and jobsite data can be recorded, displayed, analysed, managed and evaluated in one central location. The collected data can be accessed via a web browser when an internet connection is active. With the recorded PDE data, a working protocol is automatically generated as proof of quality directly after completion of a work process. The parameters of the driving protocol can be defined and assigned in advance, resulting in significant time-saving.
The LiDAT data transmission and positioning system enables the fleet management of Liebherr machines. The system supplies information about localisation as well as the operation of the machines. This includes the machine position, operating and utilisation times, fuel consumption and service interval information.
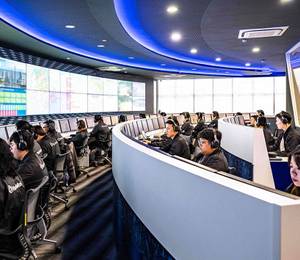
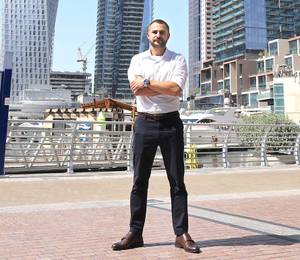
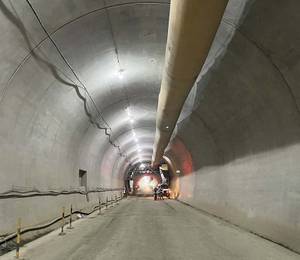
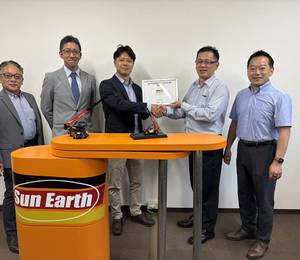

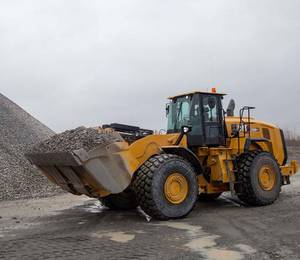

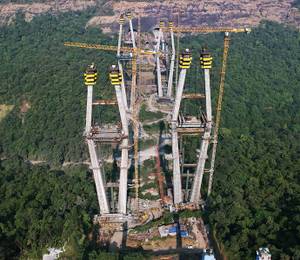
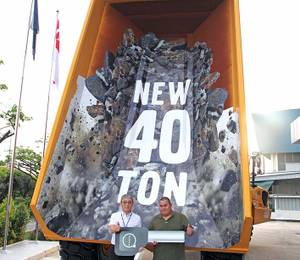
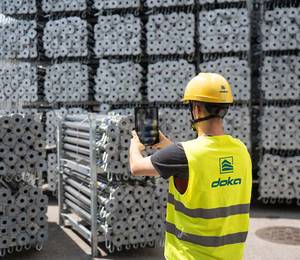